Forget about 3D printers, the AMR-X models are the result of hand work. The process is similar to that of jewelry. And throughout his career André-Marie Ruf has almost always followed it. It is summarized below.
The pictures below are showing different models. We do not have an image of a single reproduction throughout the process (the wax masters vanishes along the way – see below).
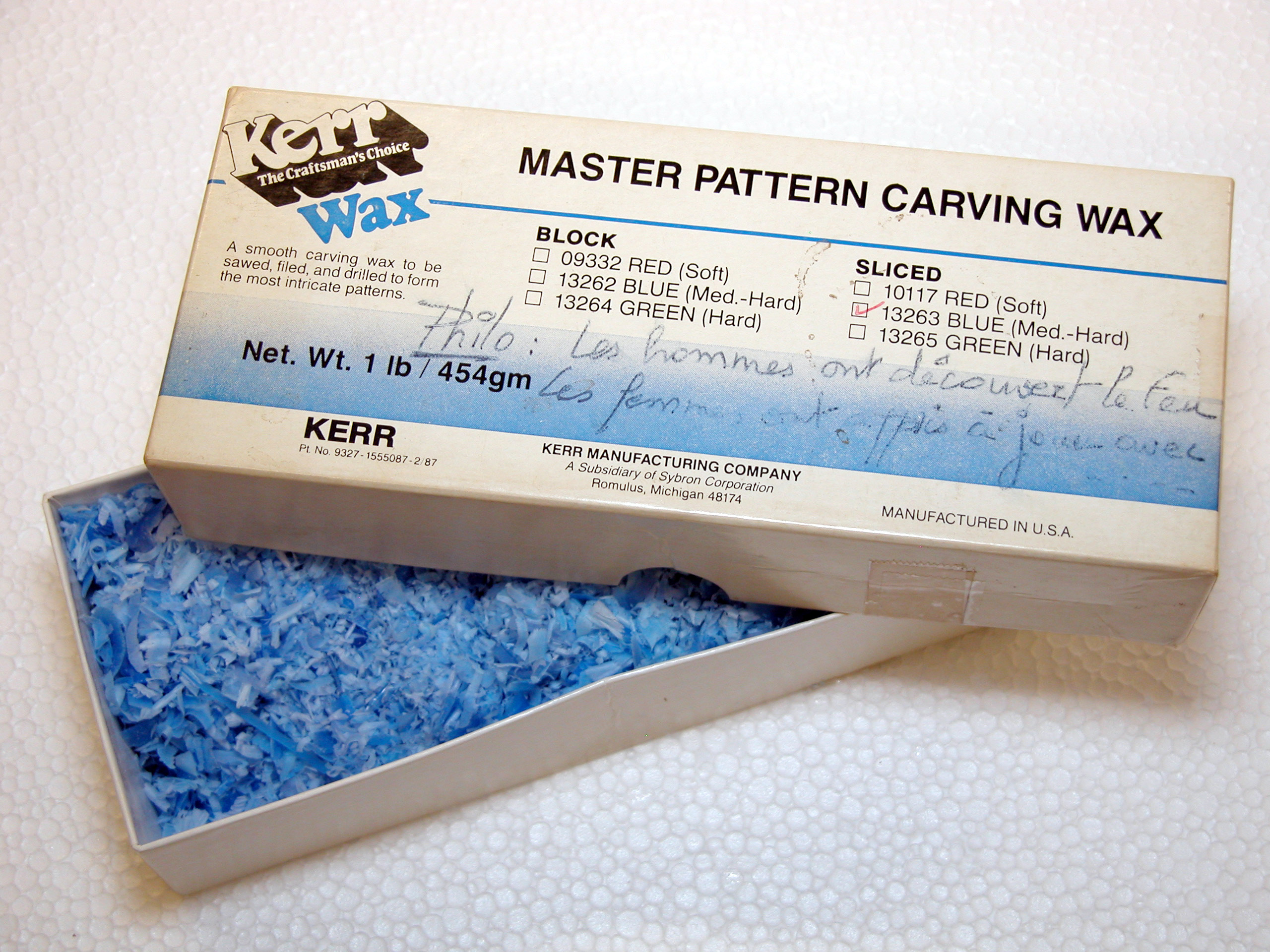
It all starts with the choice of the model to reproduce, a statement of dimensions and a well documented photo file.
The illustration below shows a characteristic inherent in this manufacturing method. To have a white-metal at 1/43, you must produce a wax at 1/41, because of the shrinkage when molding.
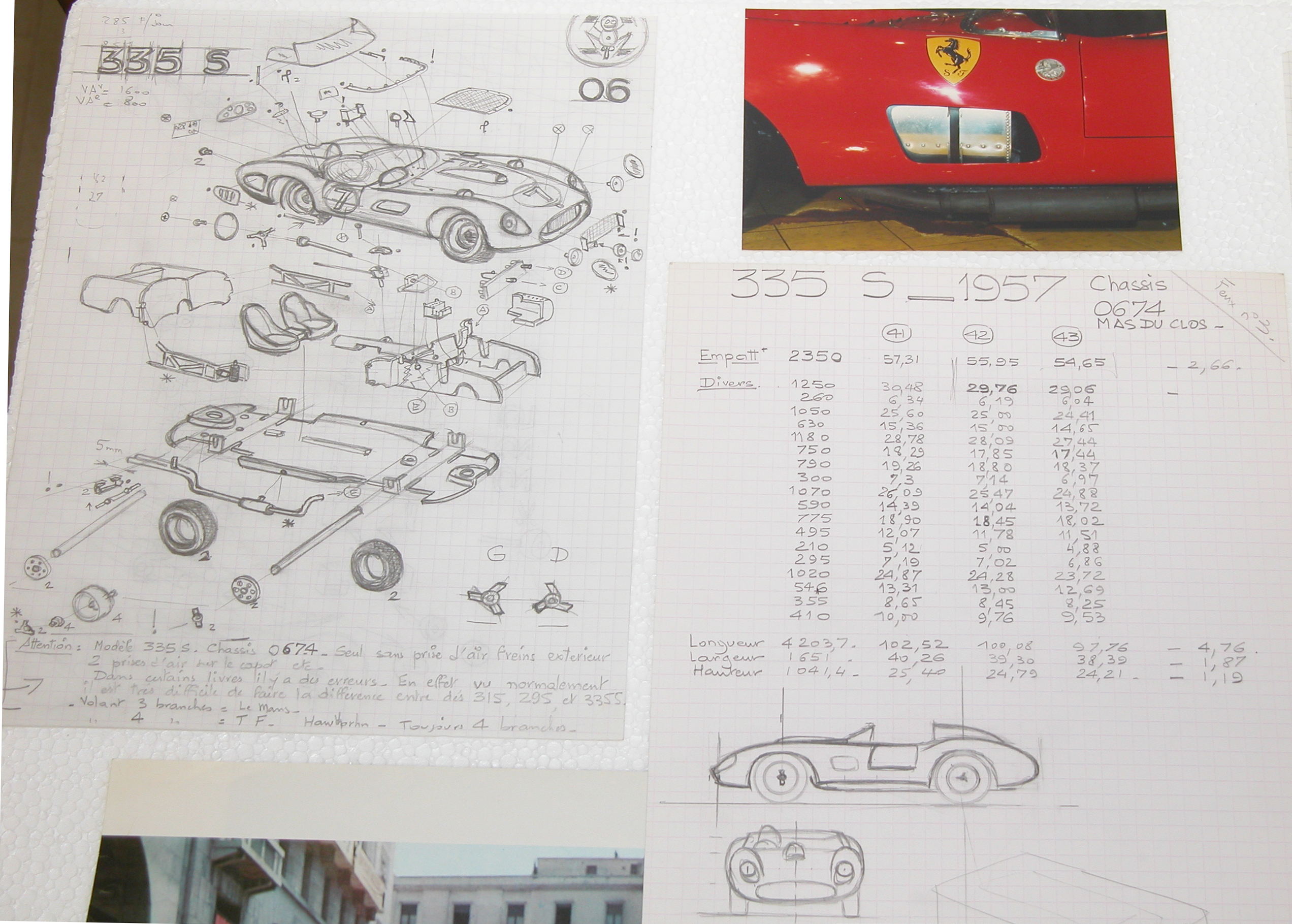
Then comes the sculpture work in a block of wax. Files, soldering iron, marble and trusquin are the main tools used for this work which can last up to 15 days. It was at this point that André-Marie RUF exaggerated:
« The eye does not recognize the character of a car if it is strictly reduced
to 1 / 43rd. So I cheat, I produce a kind of caricature by accentuating its characteristics. «
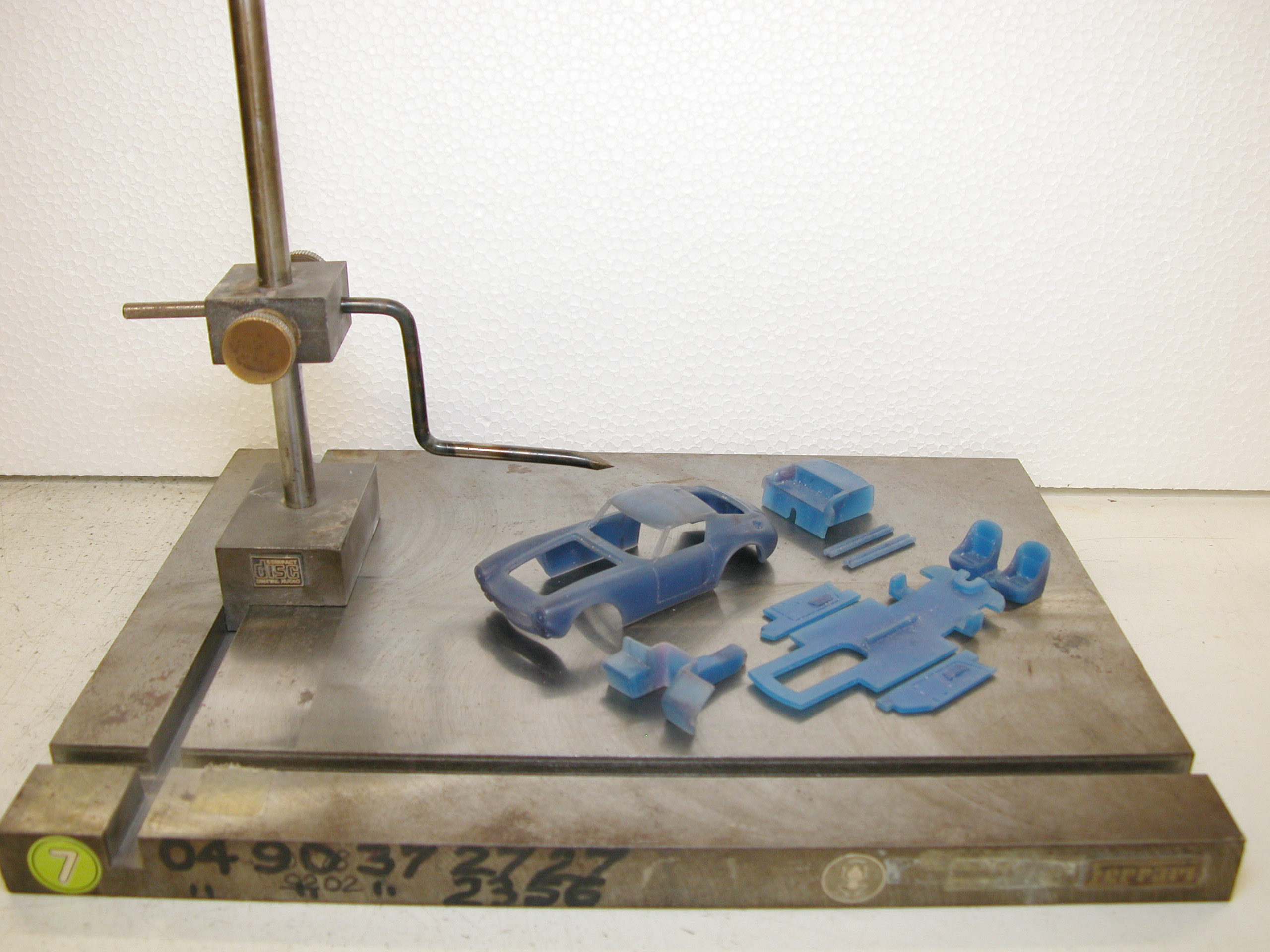
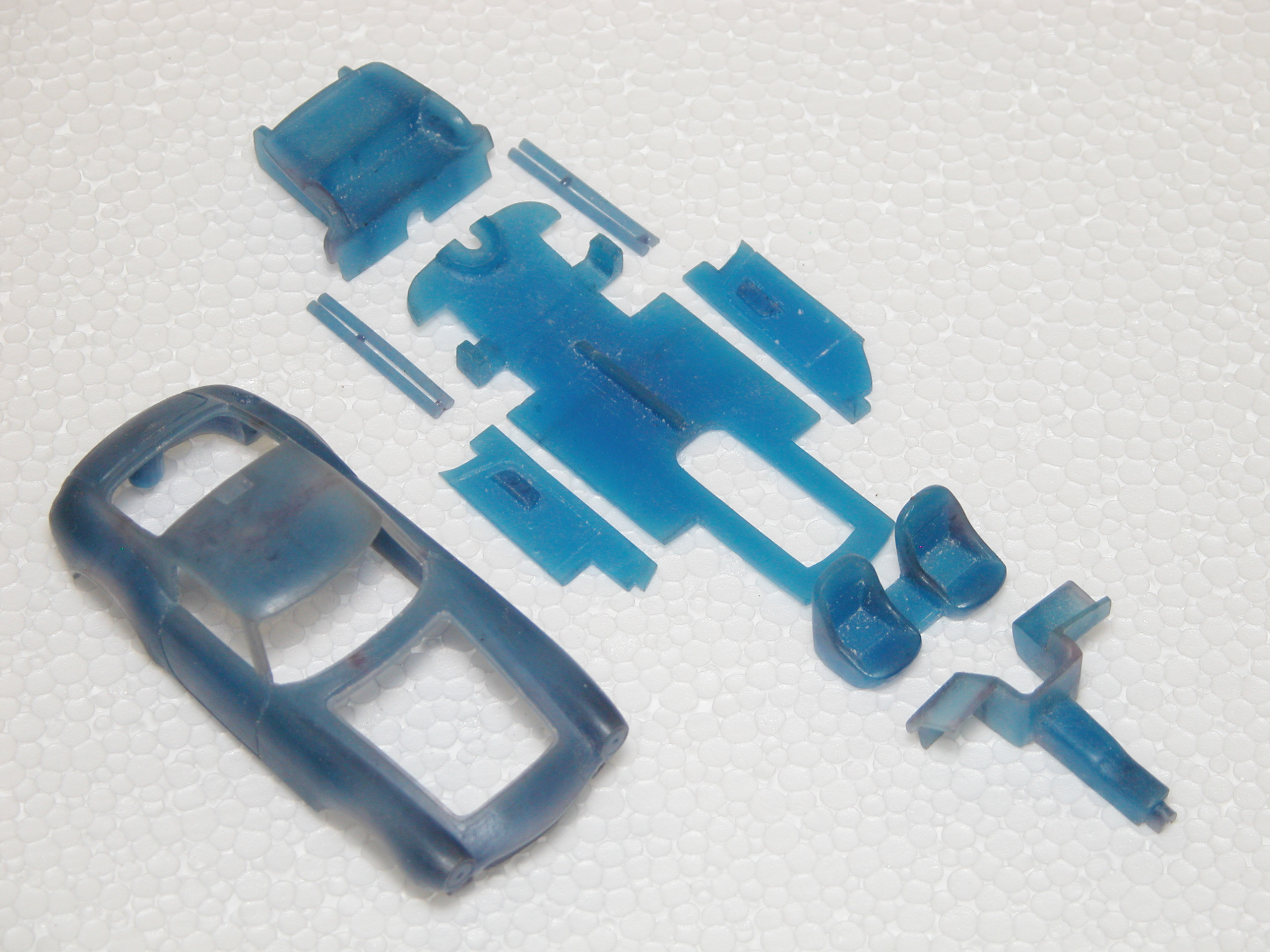
The master in wax is then transformed into brass (or bronze) by the lost wax process. Concretely, the wax pieces are put in a cylinder containing a kind of liquid ceramic. The whole is then put in the oven. The rise in temperature solidifies the liquid ceramic and melts the wax. Brass (or bronze) is poured into the hollow body left by the melting of the wax. By the way, wax to bronze means loosing a scale (1/41 to 1/42) and sometimes loosing … everything. It has happened and it has been necessary to start the wax master again.
Below is a Lusso brass master. It went out fine and could be refined.
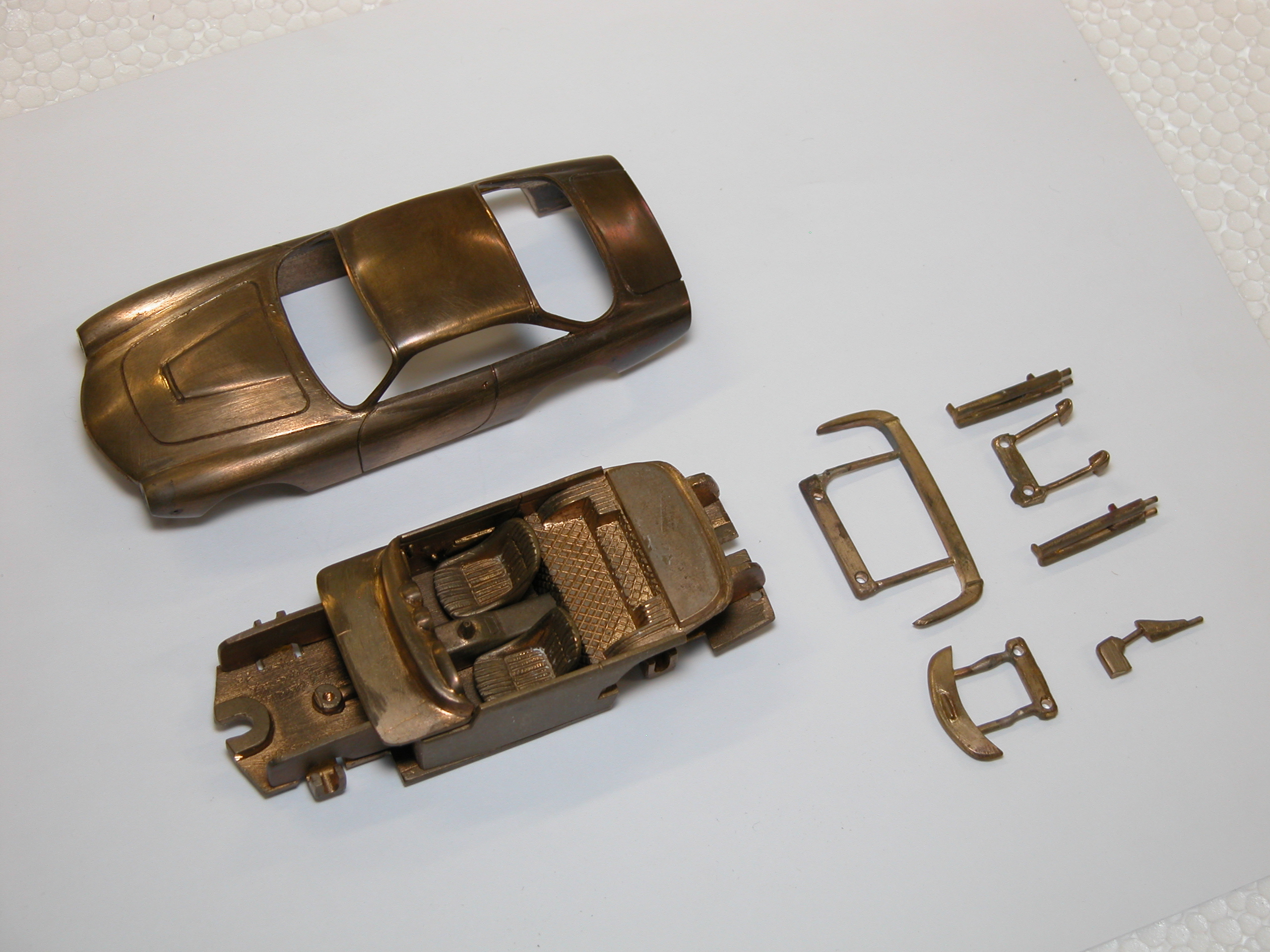
Below is an example of a fail. At least half of this Daytona is missing. However, we featured it because it is showing the typical cleaning work still necessary before molding – have a look at the front.
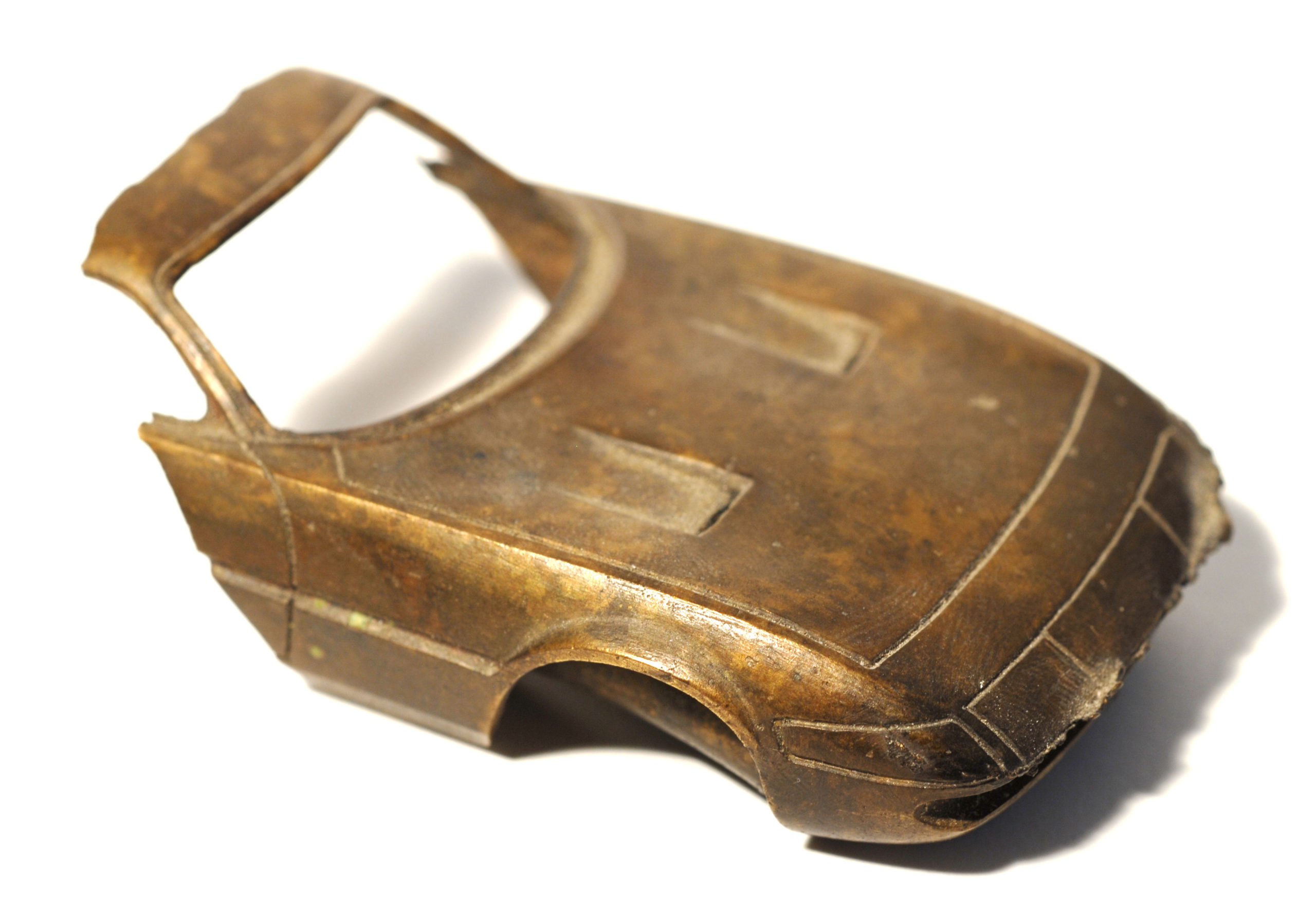
And now the production of white metal parts. The main one is the bodywork.
If brass is used, it is because it is a material resistant to the heat and pressure necessary for cooking the silicone wafers which enclose it. While baking, the silicone hardens and this hardening allows up to 360 prints.
This last molding normally produces a 1/43 model. Normally ? Yes, because since 1975 AMR-X are considered to be slightly larger. Take your calipers out if size matters to you.
The basic principle of this production of white-metal parts is centrifugal force. Just pour melt white-metal in the mold spinning fast and voilà!
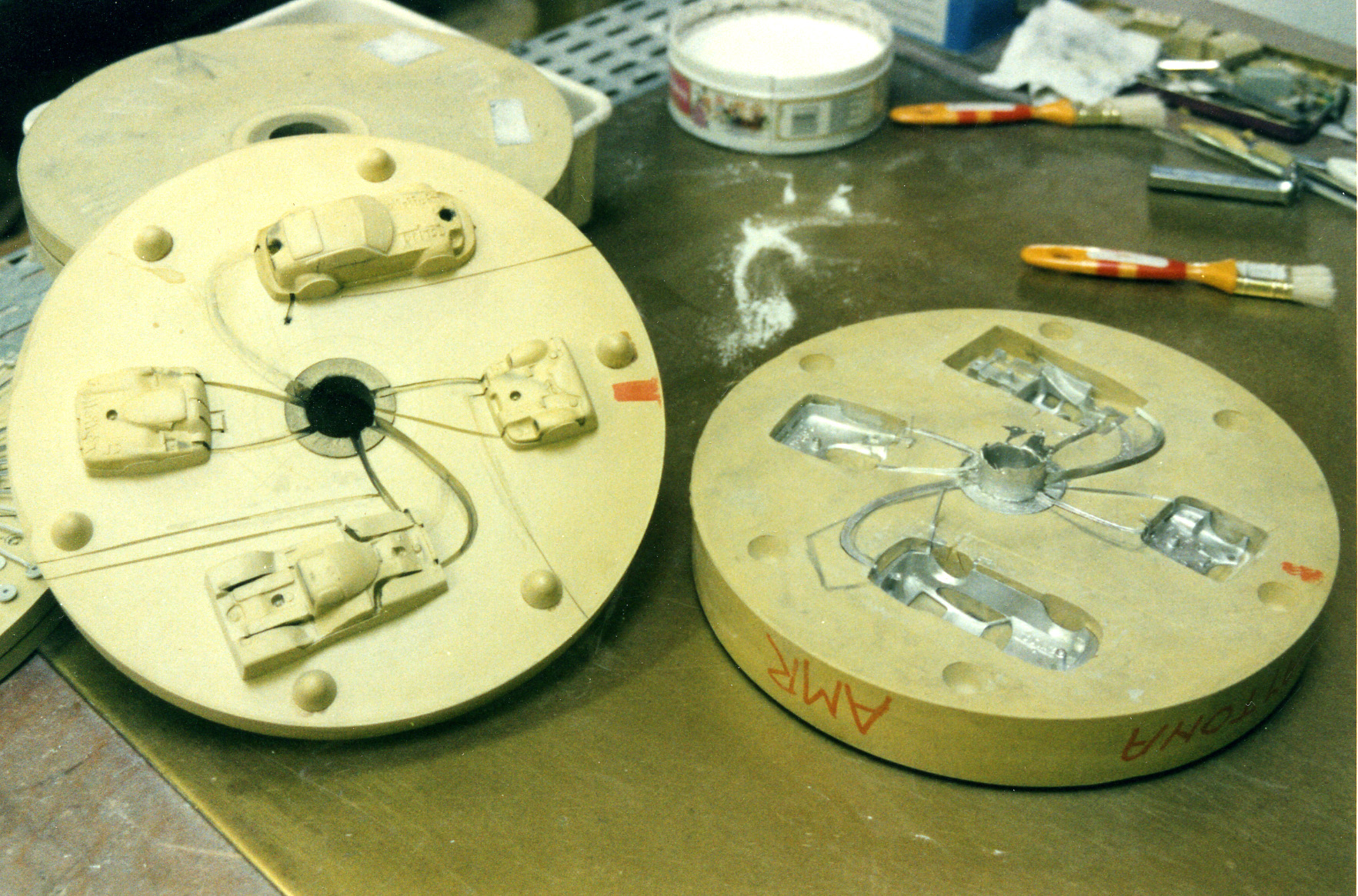
The composition of white-metal has evolved according to health regulations.
Until the mid-1980s, it was rich in lead and antimony. Gradually, the authorized share of these two materials was reduced. This is why the appearance of the kits from the 2000s is more granular. And that’s also why actual white metal parts are often brittle.
The other parts making up a kit or a factory built model were also produced using artisanal methods. AMR subcontracted the manufacture of the decals by providing a drawing of the expected. Ditto for the photoetching process. Only the molds for the vacforms were made by the team.

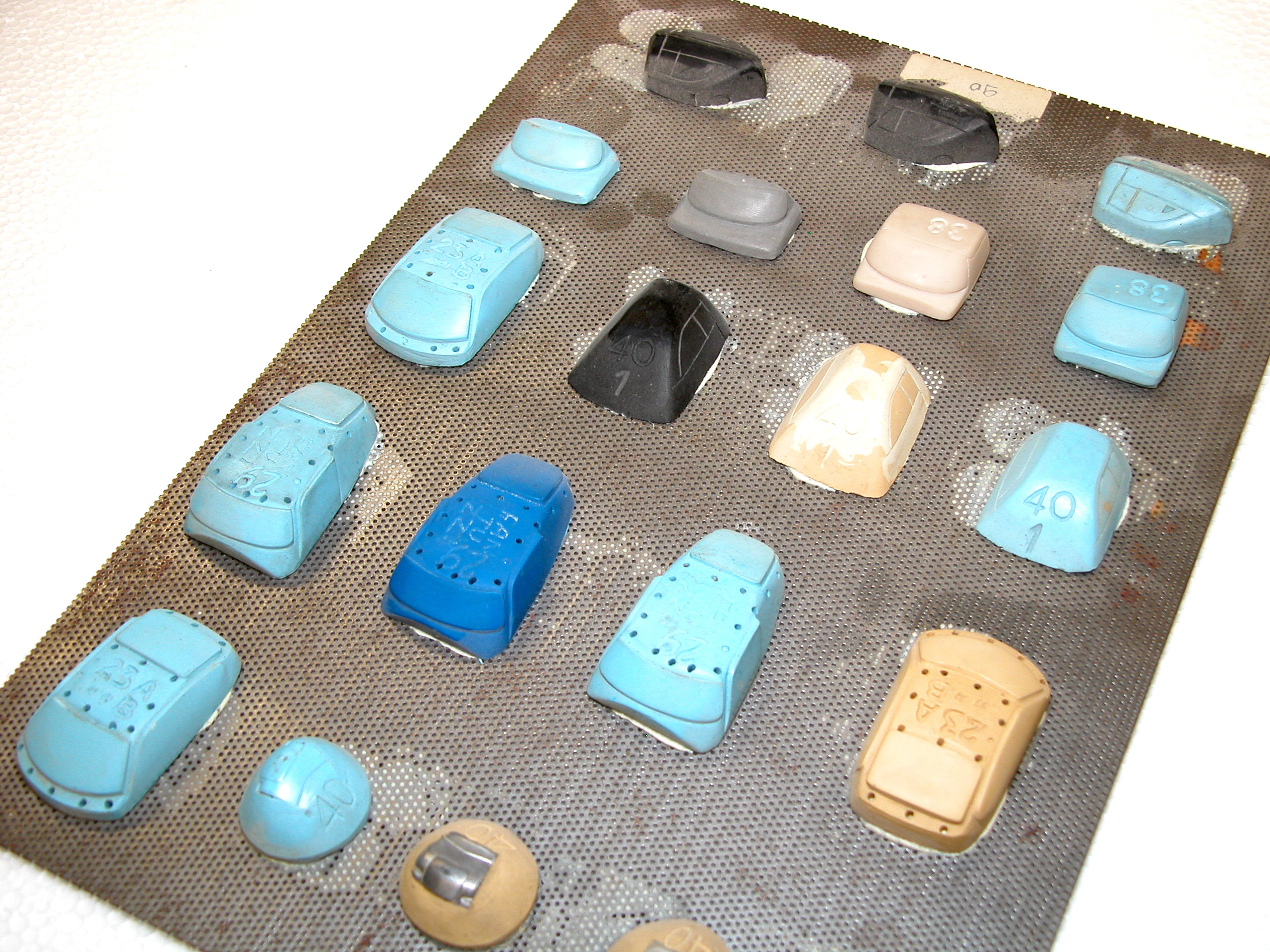
Much more could be written. This is just a quick sum-up. Hope you however have a rough idea of the whole process and understand better what makes AMR so different.